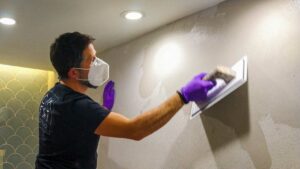
Surface Treatment for applying Microcement
Preparation of the Substrate for the Microcement Types of Substrates to Apply Microcement MICROCEMENT SUBSTRATE – One of the great advantages that microcement has compared
Polyurethane cement flooring represents one of the most advanced solutions in the field of industrial and technical coatings. Their hybrid formulation—which combines the mechanical strength of cement with the flexibility and chemical properties of polyurethane—makes them high-performance materials capable of meeting the most stringent demands in terms of durability, hygiene, and thermal and chemical resistance.
This is a continuous application system of modified polyurethane resin with cementitious mineral fillers. Unlike other systems such as epoxies or methacrylates, polyurethane cement can be applied in environments with high humidity levels and even on slightly damp surfaces, greatly expanding its application possibilities in new construction or renovations.
Its thickness can range from 3 to 15 mm, depending on the system and the level of substrate requirements. It can be applied by trowel, self-leveling pour, or with a multi-layer anti-slip system, depending on the adhesion, cleanliness, or safety requirements of the environment.
High mechanical resistance: withstands intensive road traffic (pallet trucks, forklifts), punctual impacts, and high static loads.
Excellent chemical behavior: withstands attacks from acids, alkalis, greases, oils, and aggressive cleaning agents.
Thermal stability: some cementitious polyurethane systems withstand temperatures of up to 120°C continuously and thermal shocks exceeding 150°C, making them ideal for washdown areas or industrial kitchens.
Impermeability and hygiene: the seamless, continuous finish prevents dirt buildup and facilitates cleaning. Furthermore, they can be formulated with antimicrobial properties.
Moisture resistance from the substrate: one of the main advantages compared to epoxies, which require completely dry substrates for proper adhesion.
Polyurethane cement flooring is especially suitable for sectors with high technical demands, such as:
Food industry: processing areas, cold storage, industrial kitchens, or slaughterhouses.
Healthcare and pharmaceutical sectors: laboratories, clean rooms, or operating rooms, where easy-to-clean and disinfectant-resistant surfaces are required.
General industrial spaces: production facilities, logistics warehouses, bottling plants, etc.
Demanding commercial environments: supermarkets, open kitchens, catering areas with public traffic and light machinery.
Compared to systems such as epoxy or pure aliphatic polyurethanes, polyurethane cement offers better thermal resistance, greater tolerance to moisture, and a better response to mechanical and chemical shocks. Furthermore, it allows for faster application, even on substrates with some residual moisture, which speeds up construction times and reduces downtime in industrial environments.
Proper substrate preparation, using milling or shot peening, is essential to ensure good adhesion. Ambient temperature and humidity must be taken into account, although the system is more tolerant than other resins. Furthermore, mixing, application, and curing times are essential to ensure the final properties of the pavement.
At Lunik, we understand that technical performance is not at odds with sustainability. Many cementitious polyurethane systems have a low VOC content and a long service life, which translates into fewer replacements, less waste, and a lower environmental impact throughout the pavement’s lifecycle.
To learn more about the world of continuous coatings, visit our Lunik website.
Preparation of the Substrate for the Microcement Types of Substrates to Apply Microcement MICROCEMENT SUBSTRATE – One of the great advantages that microcement has compared
Microcement and Plasterboard Plasterboard and Microcement: Great Result PLASTERBOARD AND MICROCEMENT – Plasterboard, a widely used material in construction, has gained popularity in recent decades
Microcement and Moisture Humidity and Microcement: Ensuring a Perfect Application MOISTURE AND MICROCEMENT – Humidity is one of the primary challenges when applying microcement. While